
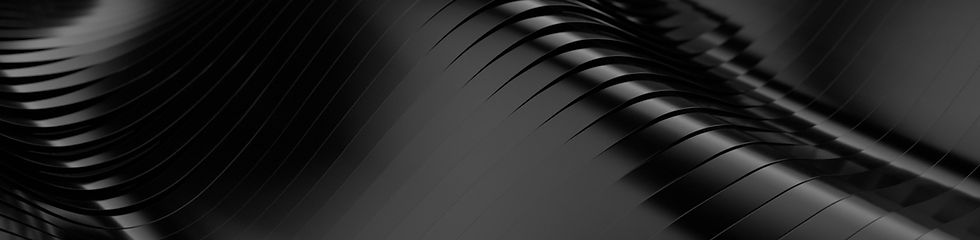
PVD & DLC
Coating's
FOR BEARINGS
Physical vapor deposition (PVD) coating processes are used in many industrial fields to improve the surface properties of metallic components and tools. Due to the high hardness and low friction values obtained by PVD coatings, the reduction of wear rates and the protection against fretting and sliding fatigue are the main drivers for the application of this kind of technology.
The importance of PVD coatings for rolling bearings being used in the aerospace industry. High-speed rolling bearings are part of turbine engines. In these bearings, two different applications of PVD coatings are applied for the generation of suitable surfaces. Tungsten Carbide WC/C or Ta-C is a hard, wear-protecting coating and is applied on the land-riding surface of rolling bearings to give enhanced reliability against fretting and severe damage in the case of bearing failure.
Coatings with good friction properties (0.01-0.03) are often demanded on rolling elements of aerospace bearings. other Examples for these kinds of coatings are diamond-like carbon and molybdenum disulfide-based coatings which are used as simple coatings that are commonly used depend in the type and quality of the coating. With the industry's and technology's moving so quickly now there are replacements of MOS2 that are tremendously more useful stronger as well as providing better coefficient of friction properties 0.01. These coating techniques that are primarily used in ARC evaporation and magnetron or sputtering vessels.
PVD Coatings
AlTiN | TiAlN | AlTiSiN | AlCrN | AlTiCrN | TiN | TiN+ | ZrN | CrN | TiCN(R) | TiCN (G) | Alcrona | Alcrona (Si) |
​
Specialty coatings : please contact us for more info

Important Tech Information
Bearings often suffer from severe and disproportionately distributed abrasive wear. A coating such as Ta-C or WC/C as well DLC coatings is particularly suitable for case-hardening and roller-bearing steels all because it can be applied at temperatures between 200C-500C
The PVD coating can be applied not only to inner and outer races and cylinders but also to the balls in ball bearings in a highly uniform coating thickness of 0.5-1 μm. The slight increase in roughness is offset by the good burnishing qualities of the coating, which smoothest the raceway of the inner and outer rings, providing additional protection against scuffing and pitting.
Bearings in the soft calendar rolls of paper machines frequently experience smearing. Not only does PVD coating reduce the possibility of smearing, but by making the bearings harder with coating, it has been shown that the life of these parts can be increased by a factor of three or four. As a result, paper mills are able to hold off on bearing replacement until the calendar roll needs regrinding, significantly reducing costly production downtime.
Similarly, cylindrical roller bearings in compressors are often exposed to low loads and vibrations, causing potential smearing. Applying PVD coating to the bearings removes any such possibility.